Patented Robotic Tape Inspection Station
To solve these issue for our customers, we developed a small footprint, high-speed robotic tape inspection station that is integrated into the end of line conveyor. The robot inspects each case quickly for tape tails.
This type of error proofing system is easily cost justified for Return on Investment by calculating the current cost to your facility of incorrectly sealed or unsealed cases based on:
- Production loss
- Product damage
- Reshipping of damaged product
- Employee time involvement
- Clean-up
- Customer Complaints
- Resolving other issues
Why Do Case Sealers Fail?
Case sealers fail when they have not been properly setup. These are some of the most common reasons for tape issues:
Stretched Tape
This can happen if the tape is installed incorrectly, the tension knob has been set too high, or the rollers are not moving freely. Tension from the stretched tape can cause tape tails to release.
Wrinkled Tape
The opposite issue of the tape being too tight can cause wrinkled tape that may not form proper tape tails. Other causes for wrinkled tape are adhesive buildup on the rollers or knife that cuts the tape.
Off-Center Tape
This is another tape installation or system alignment issue that causes the tape to miss sealing the case opening/seam altogether.
Tape Not Sticking
Tape manufacturers can mess up and there is no, or ineffective adhesive applied. Also in areas that may have excess dust cases may be too dirty, and the tape doesn’t stick properly.
Not Long Enough Tails
If the sealer isn’t properly cutting the tape and applying the overlap properly, then the case will have short tail leads and case ends are not covered over with tape.
Overfilled Cases
If cases are overfilled with bulk packed product, the flaps may not close completely and the taper will not be able to seal the flaps shut. Installing an in-line shaker table or changing the funnel that fills the cases to distribute product more evenly inside the case may improve taper performance in this instance.
Options for Robotic Tape Inspection Station
- LRMate 200iD/7L– The FANUC LRMate robot is durable, reliable, and flexible. The 7L is the long arm version with a reach of about 1 meter /36 inches
- M-10iA– The M-10iA can be used to increase reach to 2 meters/ 79 inches.
- CRX-10iA/L– Various collaborative robots can be used for tape inspection, but rate is reduced. So, it would need to be a lower throughput area.
This tape inspection station is a standalone unit like a pallet dispenser that can be a drop-in unit with very little interface required. The end of arm tool is a custom designed wand that is programmed to find tape tails. Based on the rate that is needed, you can select to test just the top or bottom seal tails. Or choose to test just the trailing or leading tail sides. Testing both tails takes about 50% longer to read and pass the case.
What Case Sizes Can be Inspected?
From small to tall cases there is a setup that can make it possible. This station inspects random case sizes and random case position on the conveyor. First each incoming case is dimensioned using a camera and sensor together. Next, the case is inspected for tape tail placement as the case passes by the robot. Using a robot gives extra flexibility because cases can come into the station skewed without any problem. Unlike stationary scanners, the robot finds the tape tails. For high speed tape inspection, there is the option for popups for squaring cases before they enter the tape inspection station allowing for a quicker read.
Transparent Tape, the most economical tape on the market, can be read using this technology. There is no minimum tape width needed and tape tail length required is 2 inches.
The proper camera/sensor combination is selected based on your needs. There are cameras available to allow an unlimited size of cases to be inspected on the same line. There is also the ability for easier setup if you have a single case or limited number of case sizes that goes through the system.
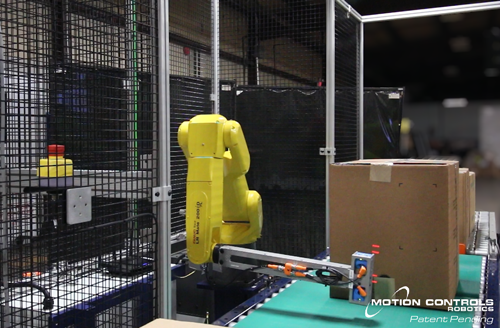
What Happens if a Case Fails?
Alarm is Triggered
If a case fails it can trigger an audio/visual alarm and the package can be handled by an operator. This scenario assumes few errors will occur each day.
Case Diversion
For dealing with high rate systems, the outgoing conveyor from the tape inspection can have a spur allowing the correctly taped cases to move on to the palletizing area while the cases with no tape tails detected can move back to the case sealing area to be manually dealt with or re-ran through the sealer.
MCRI is on the tape inspection case. If you have had similar issues with tape failure, we can look at adding a tape inspection station to your end of line operations.
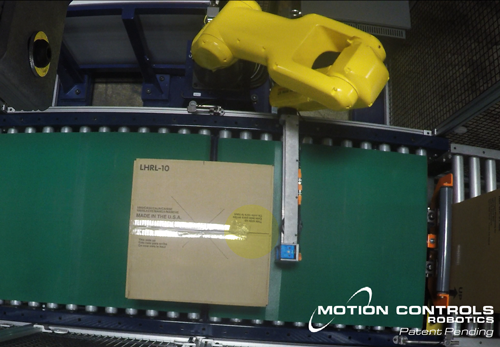
On November 21, 2023 the tape inspection station received a patent from the United States for a unique, automated case handling system. Our system is one of a kind with the added benefit of being easy to add to any current packaging line. You can view the Patent here to learn more technical information about the setup.