ASRS – Transforming Industrial Efficiency
Automated Storage and Retrieval Systems (ASRS) are at the forefront of revolutionizing storage facilities from simple storage locations to highly dynamic hubs. In today’s fast-paced industrial environments, efficiency and precision are on everyone’s mind. Our Robotic Automated Storage and Retrieval setups are a perfect example of how you can enhance operational capabilities in both manufacturing and distribution facilities.
What is ASRS?
Automated Storage and Retrieval Systems (ASRS) are technologically advanced systems designed to automate the storage and retrieval of items within a warehouse or manufacturing facility. Utilizing robotics and real-time data, ASRS solutions such as the one featured in this video improve space utilization, increase efficiency, and reduce operational costs.
The Robot at the Center: Precision and Efficiency
At the center of this hub is a FANUC M-410iB/140H robot, known for its extensive 9 feet reach and a payload capacity of 140kg. This robot model enables the system to handle both heavy and light items, storing them across 161 tote positions. The system can manage up to 215 totes per hour, showcasing its efficiency and speed.
Key Features of ASRS Automated Storage and Retrieval Systems
🔩 Precision Engineering
Robots provide consistent accuracy in locating and handling items, reducing the incidence of errors. As the end-of-arm tooling (EOAT) engages, sensors check each requested slot for availability, ensuring every part is accurately placed and retrieved without errors.
🏭 Adaptability
Each system can be tailored to meet the unique storage and space requirements of the facility. The ASRS is designed to adapt to various manufacturing and distribution needs.
Basic Uses of ASRS in Manufacturing
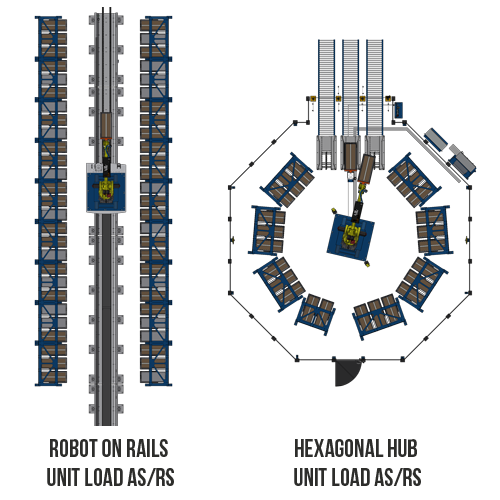
- Raw Material Storage: ASRSs can store raw materials close to production lines. This reduces material handling time and costs. Raw materials are readily available when needed, which helps to maintain a consistent production flow.
- Work-in-Progress (WIP) Storage: During different stages of the manufacturing process, partially finished goods need to be stored temporarily. Automating the storage and retrieval of these items makes the production process more efficient by reducing wait times and handling costs.
- Finished Goods Storage: After production, finished products can be stored in an ASRS before they are shipped to customers. The systems organize inventory efficiently, making it easier to manage stock levels and fulfill orders promptly.
Basic Uses of ASRS in Distribution Centers
- Order Fulfillment: ASRS are highly effective in order picking operations. They can rapidly retrieve items and deliver them to picking stations, speeding up the fulfillment process and reducing errors associated with manual picking.
- Returns Processing: ASRS can assist in sorting, storing, and retrieving returned items, which helps in quick reintegration of returns into inventory.
- Inventory Management: By automating inventory storage, ASRS enhances accuracy in inventory tracking and management. They reduce the likelihood of human error, ensuring that inventory levels are precisely maintained and updated in real-time.
🕦 Time Efficiency
One of the standout benefits of the ASRS is its contribution to time efficiency. Swift and error-free retrieval minimizes downtime, ensuring operations are seamless and productivity is maximized.
🎯 Improved Space Utilization
Utilizing vertical space transforms any storage facility into a compact powerhouse. This optimization allows facilities to expand storage capacity without the need for additional square footage. Which today is averaging $125 to $300 a square foot.
📈 24/7 Operation
The ASRS operates continuously. This non-stop operation is essential for meeting high-demand periods and maintaining constant productivity, which is critical in today’s 24/7, fast-paced environments. As an extended benefit, by automating storage and retrieval tasks, robots reduce the need for human interaction in potentially hazardous environments.
💻 Real-Time Management and Integration
The system includes an intuitive, user-friendly interface that allows for real-time inventory management. Facility managers can track and trace every item with precision, using barcodes to monitor the movement and storage of products within the system. Moreover, the integration capabilities with Warehouse Management Systems (WMS) and Enterprise Resource Planning (ERP) systems through ImpactIQ creates a seamless flow of information across all platforms.
🏅 Scalability and Future Growth
A distinguishing feature of this ASRS solution is its scalability. Starting with a single hub, facilities can add more hubs as their needs grow. This scalability ensures that integrating additional storage capabilities causes minimal disruption to existing operations and requires a small learning curve for employees.
Diverse Robotic ASRS Configurations
The versatility of Automated Storage and Retrieval Systems (ASRS) is exemplified by the diverse range of robotic configurations available to modern industries. These robotic systems are designed to optimize operations, enhance precision, and maximize storage efficiency in various environments. Automated Storage and Retrieval Systems (ASRS) are versatile in their application, with a variety of configurations designed to meet specific industry needs and spatial constraints. Below are some common types of ASRS setups, including the hexagonal hub featured in the video.
Types of Robotic ASRS Setups
- Robotic Unit Load ASRS: Robots on rails pick large items like cases or drums from vertical shelving areas.
- Robotic Mini Load ASRS: Mini load systems utilize robots on rails to handle items such as cases, totes, or cartons.
- Robotic Vertical Lift Modules (VLMs): In this configuration, the trays move to the robot, which then retrieves or replaces the requested tray, case, or carton.
- Robotic Carousel Systems: Both horizontal and vertical carousel systems can be automated with robot arms to enhance their efficiency.
- Hexagonal Hub ASRS: A standout among robotic ASRS configurations, the hexagonal hub system features a central robot surrounded by storage locations in a hexagonal layout.
See other Automated Warehouse & Fulfillment Solutions from MCRI
The innovative deployment of ASRS in industrial settings shows the power of automation in enhancing efficiency and precision. These systems not only streamline operations but also can offer substantial cost savings and space utilization improvements. As industries continue to evolve, the adoption of ASRS technologies represents a significant step towards future-proofing operations and maintaining competitive advantages. By integrating ASRS, you can achieve unparalleled operational efficiency and agility, ensuring you stay ahead of the competition.