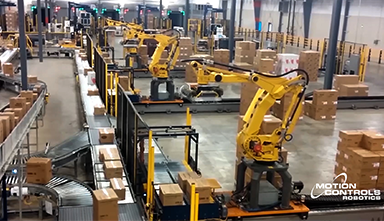
Over the past 15 years, our Unitizing Palletizer has excelled in performance. Each of the seven rail-mounted robots builds stacks at up to 18 palletizing locations along 45-foot Güdel rails. This setup allows the packaging company to sort and stack up to 80 SKUs in one facility area. Each stack is picked by a clamp AGV, delivered to a stretch wrapper, and then moved to the shipping area. Motion Controls Robotics’ Unitizing Palletizer, featuring FANUC robots on Güdel rails, has traveled an astounding 300,000 miles—farther than a trip to the moon! This milestone underscores the groundbreaking impact of advanced automation on the palletizing processes and operational productivity.
Reaching the Fifteen Year Milestone
Fifteen years ago Motion Controls Robotics began a journey to help a division of an international paperboard converter discover a way to remove an inefficient, out-of-date and unreliable gantry style central unitizing system and replace it with a more efficient, innovative robotic unitizing cell.
At the time, the converting company knew their current process was not expandable and would not allow the facility to grow as new SKUs were added to their production and as throughput demands increased.
The centralized robotic unitizing system MCRI designed to replace the gantry system sorted and unitized cases with a wide range of dimensions and weights. AGVs were added to transport the unit loads from the robotic unitizers and moved them to stretch wrappers. Once the unitized load had been dropped at stretch wrappers, they were wrapped and manually labeled. One key goal of the AGV system was to stretch wrap unit loads before they were ever transported on a conveyor. This keeps the unit loads as tight and uniform as possible before loading them onto over the road trailers.
The new system provided ample flexibility to adapt to new case dimensions and case unitizing patterns.
⏩Fast Forward to Today⏩
MCRI proudly announces that our unique Unitizing Palletizer, featuring FANUC robots, has surpassed 300,000 miles on their Güdel rails. Since 2009, this groundbreaking solution has redefined efficiency and reliability for this international paperboard converter.
MCRI services the unitizer yearly for regular maintenance and to update programming as needed. While at the facility this year, we got a new screenshot of the HMI statics showing the system has reached 300,000 miles on their rails with an average of 13 million robot cycles per robot!
The Maintenance Supervisor explained, “We have done an abundance of projects with MCRI and will continue to do so because of the durability, reliability and support we receive throughout the project and for the entire lifespan of the equipment.”
The Unitizing Palletizer is a prime example of the importance of partnering with reliable vendors. Güdel’s advanced rail technology provides the backbone for each palletizer, offering the stability and accuracy essential for these repetitive robotic applications. Combined with FANUC’s industry-leading robotics’ expertise, the result is a system that delivers unmatched speed, precision, and versatility in palletizing operations.
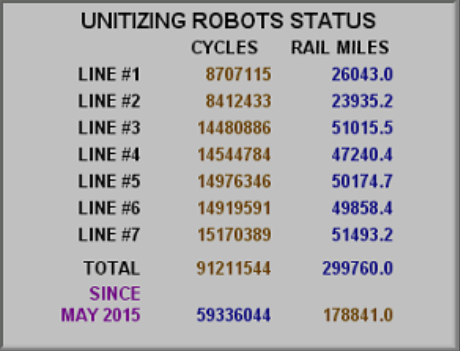
The project’s lead programmer, Eric Hohman, stated,
“This milestone is a testament to the enduring quality and durability of the Unitizing Palletizer. It demonstrates our unwavering commitment to delivering innovative solutions that exceed our customers’ expectations.”
“Overall, the biggest benefit from our new system is reliability, which was our primary consideration when we were looking for a new system. We are also excited to be using new technologies that have exceeded our original expectations in every respect.” ~ Assistant Plant Manager
The chart below shows an overview of the benefits the company experienced from the robotic unitizing system installed by Motion Controls Robotics.
Issue | Old Gantry System | New Robotic Unitizer / Centralized Palletizer | |||
Capacity /SKU Growth |
Could not keep up with current production so increasing capacity was not an option | Increased load unitizing capacity by 53% and improved production flexibility | |||
Floorspace | Located in the center of the building, away from shipping, and took up valuable production space | Located in a tight footprint next to the shipping docks, with 1200 linear feet of overhead conveyors bringing the product from production | |||
Quality | High amount of damaged boxes, inventory errors, and improperly taped boxes | Internal scrap as well as customer complaints for damaged and incorrectly shipped product were practically eliminated | |||
Safety | 1. To keep up with production, employees were manual stacking and lifting boxes as high as 85 inches which can cause repetitive motion and back injuries 2. Heavy clamp truck traffic between the gantry area and shipping posed risks for safety incidents |
1. Robotic unitizing practically eliminated need for manual unitizing labor, even with increased production and SKU’s 2. Three AGVs transport loads to automated stretch wrappers. Reduced clamp truck traffic in production areas has improved overall plant safety |
|||
Labor Costs | 1. Manual stacking required 35% of the time 2. Poor reliability meant production equipment had to be frequently shut down to supply labor for manual unitizing |
Robotic unitizers reduced labor cost for the operation by $200,000 per year by eliminating several manual labor positions across all shifts | |||
Maintenance /Reliability |
Obsolete controls, troubleshooting issues, and unavailable parts caused extended downtimes and high repair costs. | Modern PLC controls are easy to troubleshoot and replace. FANUC and MCRI have 24/7 service and support with low repair costs. Redundancy is built into the system to make sure there is little to no downtime. |
Centralized Palletizing – When is it a Unitizer?
Motion Controls Robotics has delivered numerous centralized palletizing and unitizing systems for our customers. Like central palletizing solutions, central unitizers receive case loads of product from multiple locations around the plant via conveyor, Automatic Guided Vehicle, or other material handling system, and then stack the cases into unit loads.
Unlike a centralized palletizing system, a centralized unitizing system has no pallet underneath each unit load. Benefits to elimination of the pallet include; better use of cube space for finished load shipping in over-the-road trucks; lower packaging costs, plant floor space savings, and lower automation cost since empty pallet handling is no longer required.
The 2016 Expansion
The system started with 5 robots on rails and after about 7 years, the paperboard converting company’s growing division needed even more production space at their plant site. A plant addition was planned, and MCRI was called in to relocate the existing system of 5 robotic unitizing lines and add 2 new identical unitizing lines along with additional AGVs and stretch wrappers.
The Centralized Unitizing Palletizer expansion included:
- Five FANUC M410 unitizing robots with 45’ of Gudel rail – relocated
- Two FANUC M410 unitizing robots with 45’ of Gudel rail – added
- Three clamp style AGVs – relocated
- Two new clamp style AGVs – added
- Existing end of arm tools – vacuum cups and other wear items refurbished, otherwise good working order
- Conveyors – reused some existing, added new for expanded plant operations
- Tape inspection stations – an existing station was updated with new technology, two new ones were added that incorporate all new tape sensing technology to ensure tape is properly applied to the top and bottom of each case.
- Case sealers – four new Combi random case tapers added, three existing random tapers reused
- Bar code scanners – updated scanner system to take advantage of reliability and cost savings of latest bar code technology. The scanners identify the product’s SKU to set up the random case tapers, and allow the upper level MCRI supplied PLC to track each case to an assigned SKU position from the 100+ unitizing positions available in the system
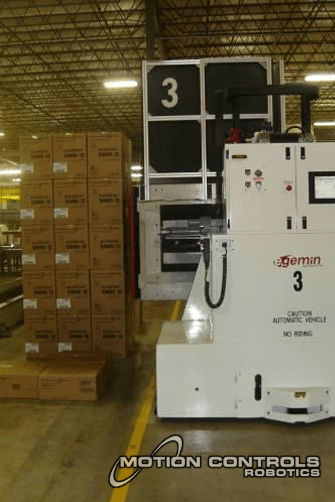
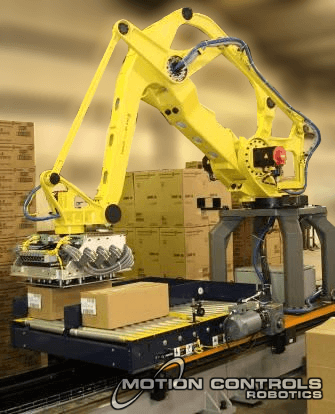