Central Palletizing Solutions for Your Facility
Central palletizing combines two or more lines by automating the transport of all products to one convenient location for robotic palletizing. This creates greater efficiency for the overall transport of product and needs fewer employees to oversee the operations. Another benefit of centralizing your palletizing operations is the sharing/optimization of equipment such as robots and wrappers.
Central palletizing saves net floor space freeing up valuable room for other operations. Another benefit is decreasing forklift traffic which increases overall facility safety.
Scenarios to look for in your facility to see if you should implement a central palletizing solution to improve operational efficiency
- Having trouble finding labor for your palletizing operation(s)?
- Is your palletizing being done in random multiple locations throughout your plant, tucked into hard to reach places, with forklifts and pallet jacks causing traffic congestion while moving packaging materials and finished pallets in different directions?
- Are you running a multiple shift operation?
- Are you shipping out multiple pallets per day from your facility?
Central palletizing systems have allowed customers to see:
- improvements in the quality of work ✓
- improved ergonomics for employees ✓
- a robust and reliable system for palletizing ✓
Central palletizing systems are highly configurable and flexible allowing for palletizing different lines with different size products.
- high throughput, low sku environment ✓
- lower throughput operation with high sku count ✓
- high throughput and high sku environment ✓
A variety of other automation can be added to the Central Palletizing location to further improve your project’s return on investment.
- Use of M-Cars/AGVs for moving product through facility
- Remote production areas connected to central palletizing by overhead conveyor
- Elevated conveyors to an overhead level
- Barcode reading for directing, tracking, and tracing
- Automated box erecting
- Case sealing with tape or glue
- Case and or tape Inspection
- Automated case and pallet labeling
- Centralized stretch wrappers
Comparing Different Options for Central Palletizing
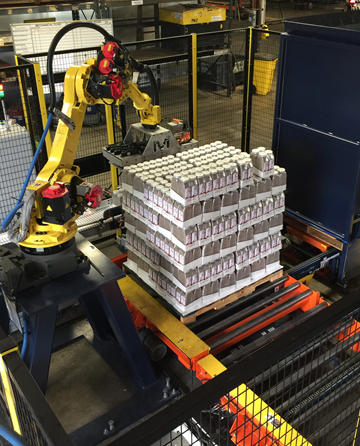
Keep it simple with four single cells:
Pros
- Simple modular design
- Less expensive end of arm tool for individual or row handling
- Easily scalable
- Each new robot is less expensive than four line palletizer
Cons
- Larger footprint for same number of SKUs
- Higher number of robots for same # SKU’s, more maintenance
- Throughput per SKU limited by robot
- Each new robot allows two SKUs
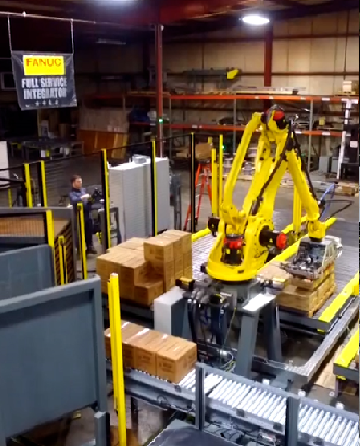
One robot palletizes four lines:
Pros
- Up to four SKUs per Robot
- Higher case rates per robot
- Fewer robots, less maintenance
- Smaller footprint for same number of SKUs
- Each new robot handles four SKU’s
- Higher SKU count
Cons
- More custom design
- More expensive end of arm tool for full layer handling
- Requires layer building on case infeed, prior to robot pick
- Throughput per SKU limited by build table

One robot using a rail:
Pros
- Rail is ideal for a combination of high SKU count and slower throughput per SKU.
Cons
- Lower throughput