Motion Controls Robotics has been installing robot systems for over 20 years, and we are starting to see customers battling with how to best handle robot replacements. Most manufacturing facilities do not want to be in the position of having an important line go down because of robot failure. When robots get older, this is a scenario that can be avoided through planning ahead and scheduling robot replacements. We wanted to give some tips to facilities about how they can handle this issue and get the most from their robots.
According to a recent BCG survey, 44% of US manufacturers are planning to install robot systems within the next five years. Many of these facilities already have robots, and are just continuing to develop their automation. As the number of robots in manufacturing facilities increase, it becomes essential to develop a plan for rotating robots either through replacement, trade-ins and/or retasking.
There are a few questions to ask when setting up a schedule for rotating robots
- How many hours a day does the robot run?
FANUC robots are tested to have reliability of more than 100,000 hours mean time between failures. So, because robots are rated by hours, some robots will run for over 20 years’ while others might start having failures in a little over 10 years.
- Has the robot been in operation for over 10 years?
For robots that have been in operation for more than 10 years and are running 24/7, it might be a good idea to look at getting a replacement for this robot. Mainly, based on a 24/7 schedule, it would be assumed that efficient, consistent production is important. Planned replacement will significantly decrease the downtime. The original robot may still be in good enough shape for trade-in or retasking in a less demanding robot cell.
- Have PM’s been done each year?
Taking care of the robot with yearly preventative maintenance extends the overall life of the robot, and decreases downtime from unplanned maintenance needs.
- What year did you install your robot?
Repair costs for robots over 10 years old become more expensive due to part availability.
Trading in a robot is a great option when developing a replacement schedule for robots
When robots currently running on a high priority line, start getting older another option is to trade-in for an upgrade. Newer robots have better safety, require less space, and are faster because of new software capabilities and innovations. So, by trading in, you not only eliminate the possibility of a failure, the new robot can increase production rates.
Some of the benefits of trading-in for a new robot with upgraded controls are:
- Product controls
- Data reporting
- Ethernet
- Dual Check Safety
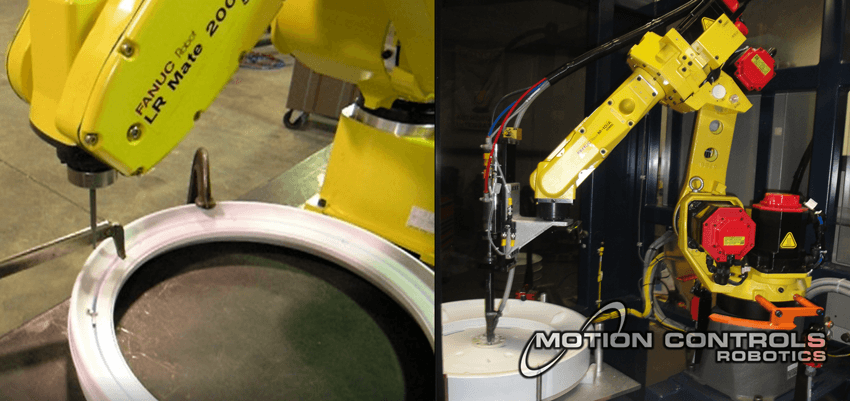
Retasking robots when production needs change
Some robots systems are designed and integrated for specific jobs that may only be contracted for a few years. Many times, when these jobs are complete, the facility just lets the robot sit. The better option would be to have an integrator stop in to see how the robot might be retasked. Retasking a robot for a new application can save money and increase efficiency while minimizing cost. Here are a couple actual examples of this being accomplished
- One plastics customer had a line with a robot that was no longer needed. We went in over a weekend and retasked the robot to pick new products with upgrades to peripheral equipment such as a new end of arm tool, pick conveyors, and controls.
- An even more involved change was when an LRMate robot was no longer needed for one job we took it in on trade for reduced purchase price on a new robot to retask a robot cell for a new operation.
- MCRI redesigned and updated a robot cell using the current robot and adding a different end of arm tool.
As you continue adding robotics to your manufacturing process, make sure to develop a plan with the goal of maximizing cost and efficiency by remembering the options to replace, trade-in and/or retask robots.